Injection Mold Manufacturers in China: A Comprehensive Guide
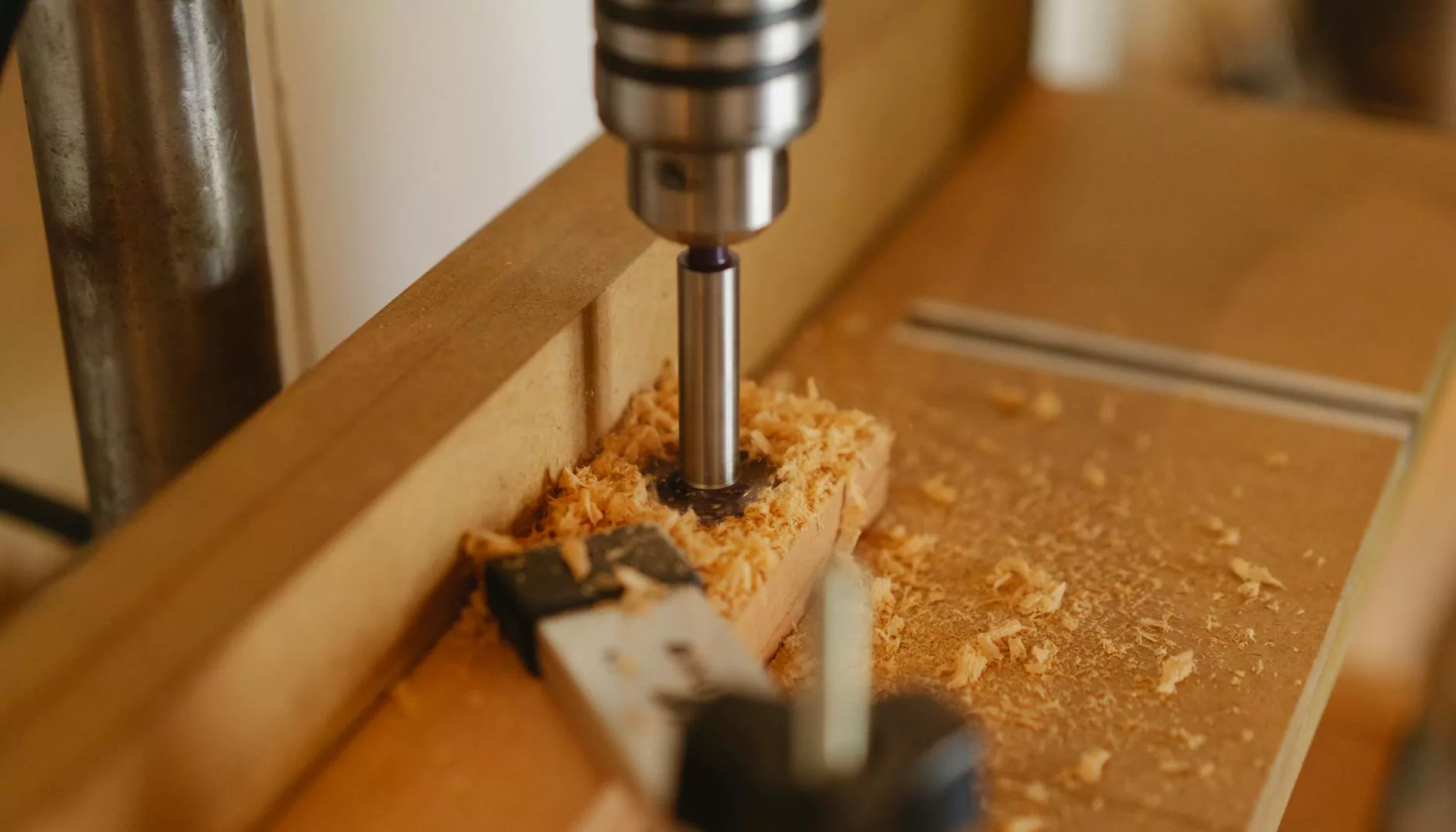
When it comes to injection mold manufacturers in China, the landscape is rich and diverse, teeming with opportunities for businesses worldwide. As a global leader in manufacturing, China is home to some of the most advanced and efficient plastic injection mold companies. In this article, we will explore the essential aspects of this industry, focusing on the benefits of partnering with Chinese manufacturers, the intricacies of the injection molding process, and tips for selecting the right supplier.
Understanding Injection Molding
Injection molding is a highly efficient manufacturing process used for producing parts by injecting molten material into a mold. This method is especially prevalent in the production of plastic components and is favored for its ability to create complex shapes at a high volume with minimal waste.
How Injection Molding Works
The core of the injection molding process involves the following steps:
- Material Selection: Choosing the right plastic resin that suits the intended application.
- Melting: The granulated plastic is heated and melted within a heated barrel.
- Injection: The molten plastic is injected into a mold cavity under high pressure.
- Cooling: The molten plastic cools and solidifies within the mold.
- Demolding: The mold is opened, and the completed part is ejected.
The Benefits of Using Injection Mold Manufacturers in China
Partnering with injection mold manufacturers in China offers several advantages:
- Cost-Effectiveness: Chinese manufacturers typically provide lower production costs due to lower labor costs and efficient manufacturing processes.
- High Production Capacity: Many factories are equipped to handle large orders, providing on-time delivery even for bulk requests.
- Advanced Technology: Chinese manufacturers often use state-of-the-art machinery and techniques, ensuring the highest quality and precision in manufacturing.
- Rapid Prototyping: Many companies offer rapid prototyping services, allowing for quick iteration of designs before mass production.
- Diverse Material Options: Manufacturers in China can work with various materials, catering to different needs and specifications.
Choosing the Right Injection Mold Manufacturer
With numerous options available, selecting the right injection mold manufacturer in China can be challenging. Here are some essential factors to consider:
1. Experience and Expertise
Look for manufacturers with a proven track record and years of experience in the industry. A company like Hanking Mould, a notable player in the field, can provide insights into their expertise in producing high-quality molds.
2. Quality Control Measures
Inquire about the quality assurance processes of the manufacturer. Effective quality control will ensure that every mold produced meets stringent standards. Manufacturers should ideally have certifications like ISO 9001 to demonstrate their commitment to quality.
3. Communication Skills
Effective communication is crucial in any international partnership. Ensure that your chosen manufacturer has personnel fluent in English and is responsive to your inquiries and concerns.
4. Technological Capabilities
A manufacturer’s technological resources can greatly impact the quality and speed of production. Assess their machinery and capability in handling complex designs.
5. Customer Reviews and Testimonials
Researching customer reviews and testimonials can provide insights into the reliability and performance of a manufacturer. Look for client feedback on platforms like Alibaba or industry-specific forums.
Common Applications of Injection Molding
The versatility of injection molding allows for a wide range of applications across industries:
- Automotive: Production of dashboards, panels, and other components.
- Consumer Electronics: Manufacturing casings for smartphones, laptops, and more.
- Medical Devices: Creation of precision components for medical equipment.
- Household Items: Production of containers, toys, and appliances.
- Industrial Parts: Fabrication of gears, valves, and machine components.
The Injection Molding Process in Detail
To fully appreciate the role of injection mold manufacturers in China, it is essential to understand the details of the injection molding process:
Material Preparation
The first step involves selecting and preparing the correct plastic resin. Materials such as ABS, polycarbonate, and nylon are commonly used due to their favorable properties.
Mold Design and Fabrication
A well-designed mold is critical for successful injection molding. Mold design involves creating a detailed CAD model, which is then fabricated using advanced machining techniques. Effective mold design considers cooling channels, ejection systems, and potential areas for defects.
Injection Phase
Once the mold is ready, the molten plastic is injected into the mold cavity. Time and pressure during this phase are crucial to the quality of the final product.
Cooling and Solidification
The cooling phase allows the plastic to solidify within the mold. Cooling time can vary based on material type, mold thickness, and complexity of the part.
Mold Cleanup and Finishing
After cooling, the mold is opened, and the part is ejected. Additional finishing processes, such as trimming, polishing, and surface treatment, may be applied to enhance the final product.
Challenges Faced by Injection Mold Manufacturers in China
While the prospects are promising, there are challenges faced by injection mold manufacturers in China:
1. Competition
The market is highly competitive, with numerous manufacturers vying for the same clients. This may lead to price wars and compromises on quality.
2. Trade Regulations
Changes in international trade regulations can impact the export of plastics and molds, necessitating constant updates and adjustments by manufacturers.
3. Environmental Concerns
The plastic industry faces significant scrutiny regarding environmental impact. Manufacturers are under pressure to adopt sustainable practices, including recycling and waste reduction.
Future Trends in Injection Molding
The injection molding industry in China is evolving, with several trends that are shaping its future:
1. Automation and Smart Manufacturing
Increased automation in manufacturing processes is leading to higher efficiency and reduced labor costs. Smart manufacturing technologies, including IoT and AI, are becoming prevalent.
2. Sustainability Practices
As environmental concerns grow, manufacturers are focusing on sustainable practices, such as using biodegradable materials and improving energy efficiency in production.
3. Advanced Materials
There is a rising trend towards using advanced materials, including composites and thermoplastics, which offer superior performance characteristics.
Conclusion
Partnering with injection mold manufacturers in China opens the door to innovation, quality, and efficiency in plastic production. As the industry continues to grow and evolve, understanding the processes, benefits, and challenges involved will equip businesses to make informed decisions. Whether you are a small startup or a large corporation, collaborating with a reliable manufacturer like Hanking Mould can significantly elevate your production capabilities and market competitiveness.
injection mold manufacturers china