Understanding Injection Plastic Molding: A Key Process in Modern Manufacturing
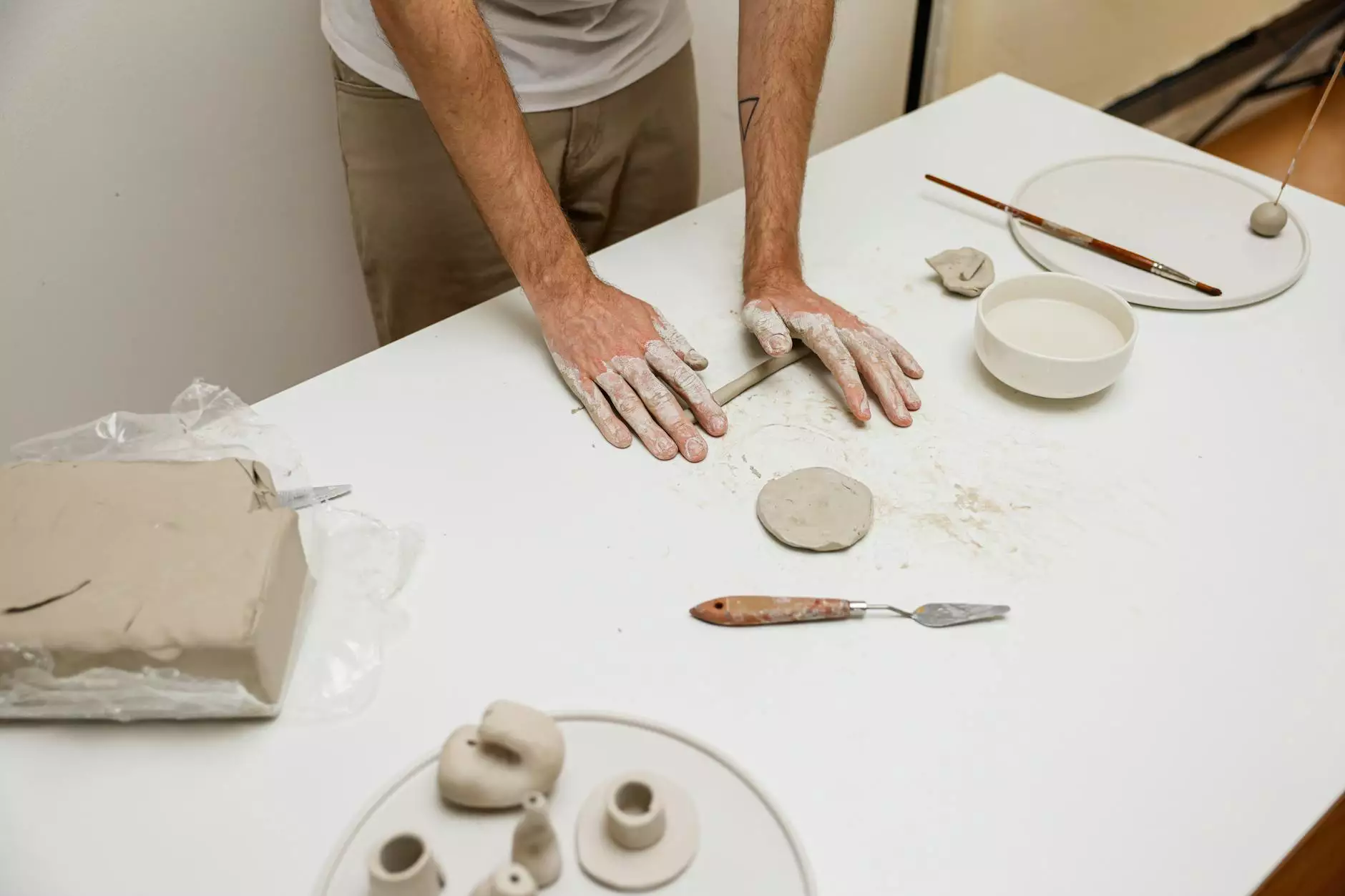
Injection plastic molding is a revolutionary process that has transformed the landscape of manufacturing. This method is essential for producing complex shapes and high-volume parts, making it a vital technology in various industries such as automotive, consumer goods, electronics, and medical supplies.
The Basics of Injection Plastic Molding
At its core, injection plastic molding involves several key steps:
- Material Preparation: Plastic pellets or granules are fed into a heated barrel where they are melted down into a viscous liquid.
- Mold Creation: A mold, designed based on the specifications of the part to be produced, is closed around the injection unit.
- Injection Process: The melted plastic is rapidly injected into the mold cavity under high pressure.
- Cooling Phase: After the plastic fills the mold, it cools and solidifies to take on the shape of the mold.
- Mold Opening: Once cooled, the mold opens to eject the finished product, and the cycle can begin anew.
Benefits of Injection Plastic Molding for Manufacturers
The injection plastic molding process offers numerous advantages that set it apart from other manufacturing methods, including:
- High Efficiency: With the ability to produce thousands of parts in a single production run, this method dramatically reduces manufacturing costs and time.
- Complex Geometries: The intricate designs that can be achieved with molds allow for versatile product shapes that are often impossible with other processes.
- Minimal Waste: Injection molding is highly efficient as it uses only the material needed to create the final product, generating less scrap compared to other methods.
- Consistent Quality: The automated nature of the process ensures uniformity and consistency in each part produced, ensuring high-quality standards are met.
- Diverse Material Options: A wide range of thermoplastics, elastomers, and even some thermosetting plastics can be used, each providing unique properties suitable for specific applications.
Applications of Injection Plastic Molding
The applications of injection plastic molding are virtually limitless, thanks to its versatility. Here are some of the primary sectors that benefit significantly from this process:
1. Automotive Industry
In the automotive sector, injection molding is crucial for creating various components such as dashboards, door panels, and interior trims. This technology allows for lightweight and durable parts that meet stringent safety and performance standards.
2. Consumer Products
Daily-use items like containers, toys, and electronics housings are commonly produced using injection molding. The ability to produce aesthetically pleasing and functional designs at scale makes it a favored choice among manufacturers.
3. Medical Devices
Injection molding plays a vital role in the production of medical devices, including syringes, surgical tools, and diagnostic equipment. The precision and consistency afforded by this method are crucial for maintaining safety and efficacy in medical applications.
4. Packaging
The packaging industry extensively utilizes injection molding to create containers, lids, and complex packaging designs that are both functional and eye-catching, enhancing product visibility on the shelves.
The Injection Plastic Molding Process Explained
Delving deeper into the injection plastic molding process, we can highlight some significant technical steps that contribute to its success.
Step 1: Material Selection
Selecting the right plastic material is critical. Choices include nylon, polypropylene, polystyrene, and more, each offering distinct characteristics like strength, flexibility, and temperature resistance. Manufacturers must assess factors such as:
- Mechanical properties
- Thermal stability
- Color and finish options
- Cost-effectiveness
Step 2: Designing the Mold
A well-designed mold is integral to the injection molding process. It should accommodate factors such as ease of part release, cooling inefficiencies, and flow of the molten plastic.
Step 3: Setting Up the Machine
The settings of the injection molding machine must be precisely configured based on the type of material used and the specifics of the mold. Key parameters include:
- Injection speed
- Temperature settings
- Pressure levels
- Cycle times
Step 4: Quality Control
Quality control is indispensable in the injection plastic molding process. Manufacturers implement various testing methods to ensure that the products meet safety standards and specifications. These methods can include:
- Visual inspections
- Dimensional measurements
- Stress testing
- Simulation testing
Choosing the Right Injection Molding Partner
Selecting a reliable partner for your injection molding needs can significantly impact your manufacturing efficiency and product quality. Here are some factors to consider:
- Experience and Expertise: Choose a company with a proven track record in diverse industries.
- State-of-the-art Technology: A company that invests in the latest machinery can offer better precision and cost-efficiency.
- Customization Capabilities: Look for partners who can offer custom solutions tailored to your specific needs.
- Strong Quality Assurance Programs: Quality is paramount in molding processes; ensure that your partner follows rigorous quality control protocols.
- Innovative Material Solutions: A good partner should offer guidance on material choices to optimize performance and cost.
Conclusion: Embracing the Future of Injection Plastic Molding
As industries continue to evolve and demand more efficient manufacturing processes, injection plastic molding remains at the forefront of innovation. Its ability to produce high-quality, complex parts in large volumes offers significant advantages for manufacturers across various sectors.
In partnering with experienced professionals, such as those at deepmould.net, businesses can tap into the full potential of this crucial technology, ensuring they stay competitive in an ever-changing market. By investing in high-quality injection molding, companies not only enhance their product offerings but also drive sustainability through efficient material use and reduced waste.