High Pressure Die Casting Suppliers: Your Ultimate Guide
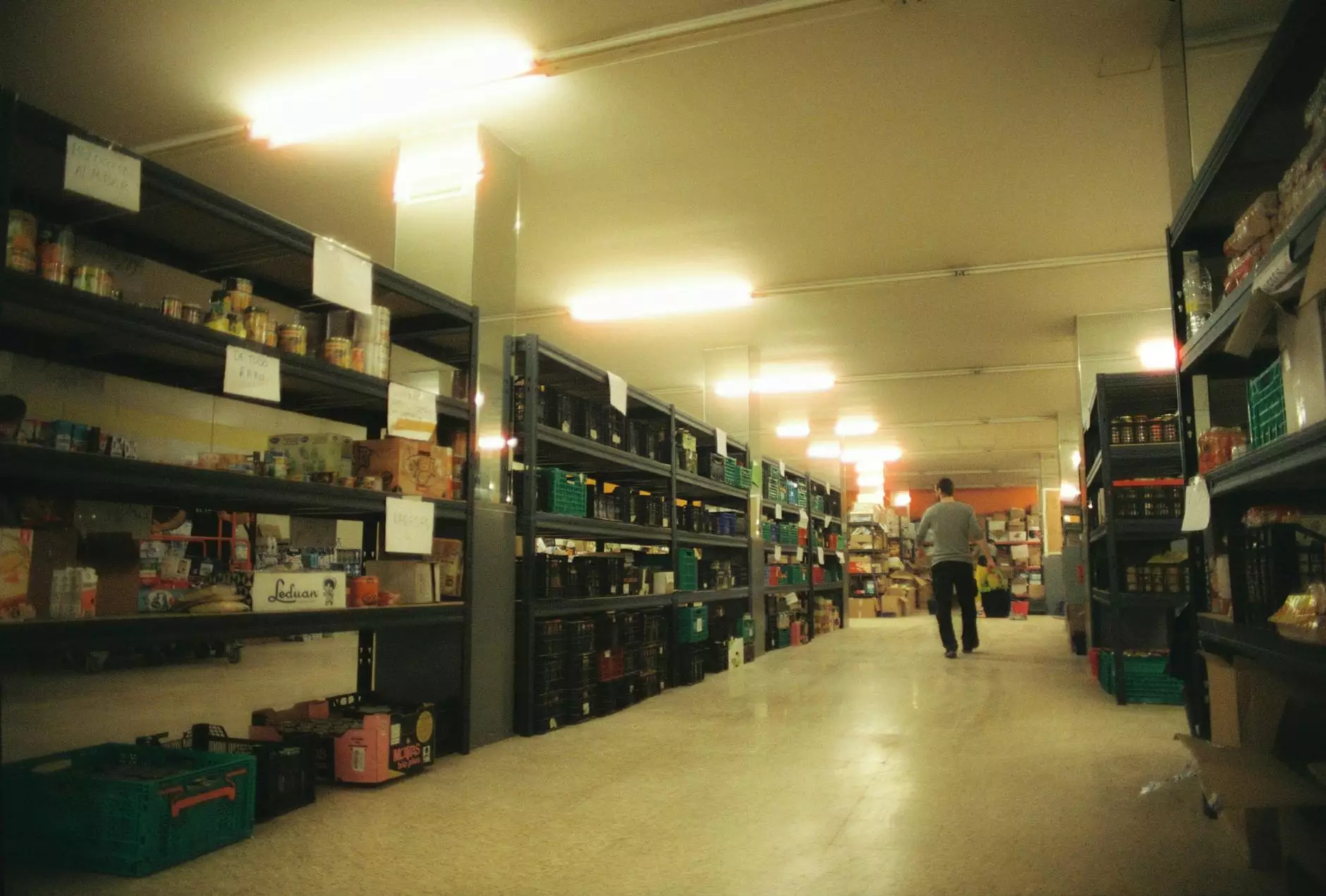
High pressure die casting is a manufacturing process known for its efficiency and precision in creating complex metal parts. If you're in the industry, understanding how to select the best high pressure die casting suppliers is crucial to achieving quality outcomes for your projects. In this comprehensive guide, we will explore the ins and outs of high pressure die casting, the importance of choosing the right supplier, and how to navigate this vital aspect of metal fabrication.
Understanding High Pressure Die Casting
High pressure die casting is a technique that involves forcing molten metal into a mold cavity under high pressure. This method ensures high dimensional accuracy and uniformity, making it ideal for producing complex parts for various applications, including automotive, aerospace, and consumer products.
The Process of High Pressure Die Casting
The high pressure die casting process involves several key steps:
- Preparing the Mold: The mold is preheated and coated with a release agent to prevent the molten metal from sticking.
- Injection of Molten Metal: Molten metal is injected into the mold under high pressure, typically between 1,000 and 2,500 psi.
- Cooling and Solidification: The metal quickly cools and solidifies within the mold.
- Mold Removal: Once solidified, the mold opens, and the part is ejected.
- Finishing Processes: The casting may undergo machining or surface treatment for enhanced performance or aesthetics.
Benefits of High Pressure Die Casting
Choosing high pressure die casting as your preferred metal fabrication process comes with a myriad of advantages:
- High Production Rates: This method allows for rapid production of parts, making it suitable for high-volume manufacturing.
- Excellent Dimensional Accuracy: The pressure used in this process ensures tight tolerances and minimal need for machining.
- Complex Shapes: High pressure die casting can create intricate designs that would otherwise be challenging or impossible to achieve.
- Material Versatility: A variety of metals can be used, including aluminum, zinc, and magnesium alloys.
- Cost-Effective for Large Runs: The initial investment in tooling may be high, but the cost per part decreases significantly with large quantities.
Choosing the Right High Pressure Die Casting Supplier
When it comes to selecting high pressure die casting suppliers, several factors come into play. Ensuring that your chosen supplier meets your specific needs can greatly affect the success of your projects.
1. Expertise and Experience
It’s critical to partner with suppliers that have extensive experience in high pressure die casting. Evaluate their track record and request case studies or examples of past projects. A seasoned supplier will understand the nuances of the process and how to handle various challenges, ensuring a smooth production flow.
2. Quality Control Measures
Quality assurance is paramount in high pressure die casting. Make sure that your supplier has stringent quality control procedures in place, such as:
- Regular inspections and testing of castings.
- Certification to international quality standards (ISO 9001, for example).
- Use of advanced technologies for quality assurance, such as 3D scanning and non-destructive testing (NDT).
3. Range of Services Offered
Choose suppliers that provide a comprehensive range of services beyond just casting. This may include:
- Design assistance and prototyping.
- Machining and finishing services.
- Logistics and supply chain management.
4. Technological Capabilities
The supplier's investment in technology can significantly impact production efficiency and product quality. Look for suppliers that utilize:
- Advanced die casting machines with automation capabilities.
- Computer-aided design (CAD) systems for precision modeling.
- Process simulation software to optimize casting processes.
5. Customer Service and Communication
Effective communication is vital for successful collaboration. Assess the supplier's responsiveness, willingness to address concerns, and their ongoing support throughout the production process.
Evaluating Supplier Performance
Once you've chosen a high pressure die casting supplier, ongoing evaluation is essential to ensure they meet your standards. Key performance metrics include:
- Delivery times and adherence to production schedules.
- Product defect rates and return rates.
- Customer feedback and satisfaction levels.
Conclusion: Partnering for Success
In conclusion, selecting the right high pressure die casting supplier is a critical decision that can impact the quality of your products and the efficiency of your manufacturing process. By considering factors such as expertise, quality control, service offerings, technological capabilities, and communication, you can find a supplier that aligns well with your business goals. At DeepMould.net, we pride ourselves on being a leading resource for metal fabrication, promising exceptional service and unparalleled quality in high pressure die casting. Embrace this knowledge, and take the step towards achieving excellence in your operations.